In industrial storage and warehousing, cantilever racking systems stand out for their unique ability to store long, bulky, or irregularly shaped items—ranging from timber and steel bars to PVC piping and furniture. This type of racking is distinguished by its arms extending from a single column, providing unobstructed storage space that can be adjusted according to the size and weight of the items being stored. However, one question that frequently arises among warehouse managers and safety officers in the UK is whether cantilever racking needs to be bolted down. This blog post aims to explore this question in depth, examining the importance of stability, safety regulations, and best practices for the installation of cantilever racking systems.
The Critical Importance of Stability
At its core, the stability of a cantilever racking system is paramount to ensuring both the safety of warehouse personnel and the protection of stored goods. The design of cantilever racks, with arms extending outwards, creates a situation where the centre of gravity is not only higher but also potentially more forward than in traditional racking systems. This configuration can lead to an increased risk of tipping if the racking is not properly anchored, especially when loaded with heavy materials. Bolting down cantilever racks significantly enhances their stability, making it a fundamental consideration for warehouses aiming to maintain a safe working environment.
Adhering to Health and Safety Regulations
In the United Kingdom, warehouse operations are subject to stringent health and safety regulations overseen by the Health and Safety Executive (HSE). These regulations mandate that all workplace equipment, including storage racking, must be used in such a way as to ensure safety and prevent accidents or injuries. While the HSE guidelines do not prescribe specific methods of securing cantilever racking, they do require that racking systems be stable and safely used. Bolting down cantilever racks is widely regarded as a best practice to meet these requirements, ensuring that the racks remain upright and secure under load, thus minimising the risk of collapse or tipping.
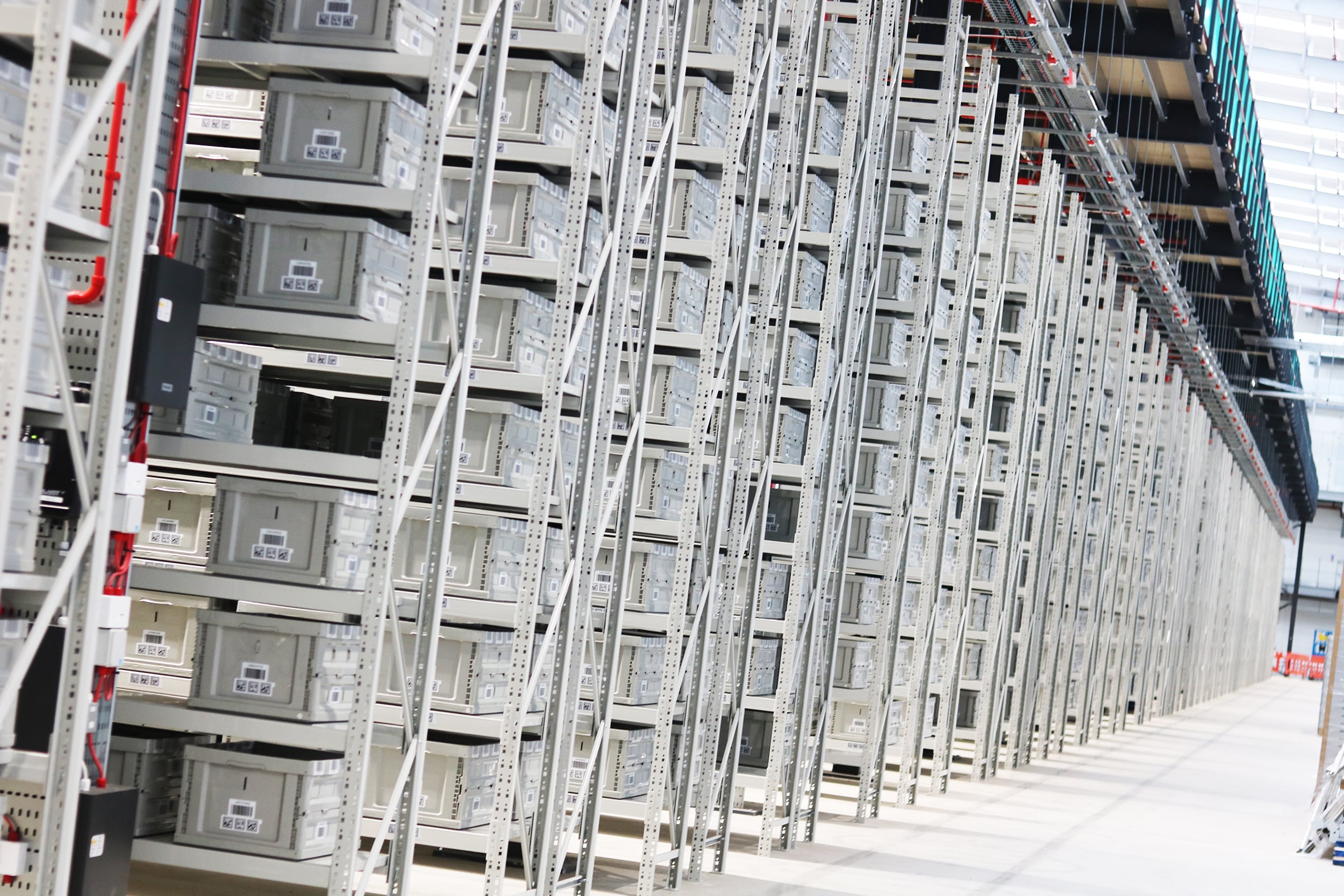
Best Practices for Cantilever Racking Installation
When installing cantilever racking, several best practices should be followed to ensure the safety and stability of the system. Firstly, the surface on which the racking will be installed must be carefully considered. Concrete floors are typically recommended due to their ability to provide a solid foundation. Prior to installation, the floor should be evaluated to ensure it is level and capable of supporting the weight of the loaded racking. Bolting the racking down into concrete not only enhances stability but also ensures that the racking remains in its designated position, which is crucial for maintaining organised and efficient storage areas.
Another important consideration is the distribution of load on the cantilever racking. The design of the system allows for the storage of long and heavy items, but these must be loaded correctly to prevent overloading the arms or creating an uneven weight distribution that could compromise the rack’s stability. Adhering to the manufacturer’s guidelines on weight limits and load distribution is essential. By ensuring that the racking is both bolted down and correctly loaded, warehouse operators can significantly reduce the risk of accidents.
The Role of Regular Inspections and Maintenance
Beyond the initial installation, the long-term safety of cantilever racking systems also depends on regular inspections and maintenance. These inspections should be conducted by trained personnel who can identify potential issues, such as loosened bolts, damaged arms or base plates, and signs of corrosion. Any identified problems should be addressed promptly to prevent further deterioration that could compromise the racking’s stability. Regular maintenance and tightening of bolts are crucial steps in ensuring that the racking remains securely anchored over time.
Engagement with Professional Installation Services
The installation of cantilever racking systems is not merely a matter of bolting down components to the warehouse floor. It involves a comprehensive understanding of load dynamics, spatial planning, and safety standards. Engaging with professional installation services ensures that the racking is installed correctly and in compliance with all relevant British Standards and HSE guidelines. These professionals can offer invaluable advice on the optimal layout of cantilever racking to maximise space utilisation and accessibility, while ensuring stability and safety. Their expertise also extends to assessing the suitability of the warehouse floor and recommending any necessary modifications to accommodate the racking system securely.
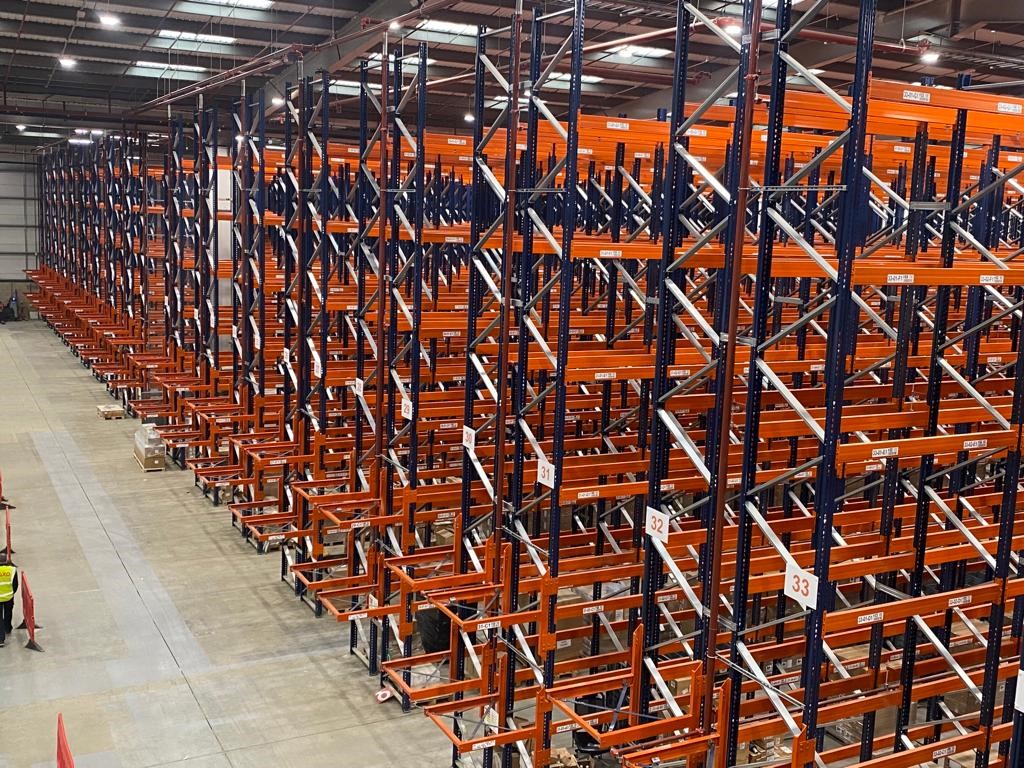
Insurance and Liability Considerations
Another critical aspect to consider is the impact of bolting down cantilever racking on insurance policies and liability issues. Insurance providers may require proof that all warehouse storage systems, including cantilever racks, are installed and maintained following industry standards to minimise risk. Failure to secure racking adequately can lead to accidents, which in turn could result in insurance claims being denied or premiums being increased due to perceived higher risks. Furthermore, in the event of an incident, the adherence to safety practices, including the bolting down of racking, could significantly impact liability determinations. Ensuring that cantilever racking systems are securely bolted and compliant with safety regulations can therefore mitigate legal and financial risks.
A Comprehensive Approach to Safety and Efficiency
The discussion underscores the multifaceted benefits of bolting down cantilever racking systems within UK warehousing and industrial contexts. From enhancing stability and safety to meeting regulatory requirements and mitigating insurance and liability risks, the practice of securing cantilever racks is shown to be a critical element of warehouse management. Additionally, the engagement with professional installation services and adherence to best practices in maintenance and load management further contribute to creating safer and more efficient storage environments. In summary, while the immediate concern might be the physical securing of cantilever racking to the warehouse floor, the broader implications touch on operational efficiency, safety culture, and risk management. For warehouse managers, safety officers, and business owners, the decision to bolt down cantilever racking should be seen as a proactive step towards ensuring the long-term success and sustainability of their operations, safeguarding both their workforce and their assets. Get in touch with the team at PD Industrial for all your cantilever racking needs.